Are you facing issues with your metal roof? Don’t worry, we’ve got you covered! In this comprehensive guide, we will discuss the most common problems that can arise with metal roofs and solutions to repair them effectively. From leaks and rust to loose panels and insulation problems, we will explore the top 11 issues that homeowners often encounter. Whether you’re a DIY enthusiast or seeking professional assistance, our guide will equip you with the knowledge and techniques to ensure the longevity and durability of your metal roof. Say goodbye to roof troubles and embrace a worry-free experience as we navigate through the solutions together. Get ready to tackle those metal roof problems head-on and safeguard your investment!
👉 11 Most Common Metal Roof Problems
#1 Oil Canning

Oil canning is an issue that occurs when a metal roof panel is over-stressed and cannot maintain a flat form. This results in visible waves and is a common problem in flat metal panels. Oil canning can occur on any type of metal panel, including steel, aluminum, zinc, and copper. The primary causes of oil canning include increased tension on the metal roofing panels, poor handling or storage by roofing contractors, inadequate space for thermal expansion and contraction, improper installation by a metal roofing company or metal roofing contractor, and damage from cutting and roll-forming metal panels during the production process.
Solution: To minimize oil canning, you can choose panels with a thicker gauge or more narrow width, add striations to the panels, and hire an expert installer to avoid faulty installation.
#2 Leaking

Leaky roofs are a building or homeowner’s worst nightmare. Metal roofs are susceptible to leaks, which can be caused by structural damage, ice dams, and installation errors. Leaks can also be caused by failed fasteners, seams, flashing, sealant, and other missed details during installation.
Solution: To avoid leaks, make sure your metal roof is installed by a knowledgeable and experienced roofing contractor. Ensure proper drainage to prevent ponding, use a high-quality underlayment, and inspect your roof after storms for damage.
#3 Scuffing and Scratching
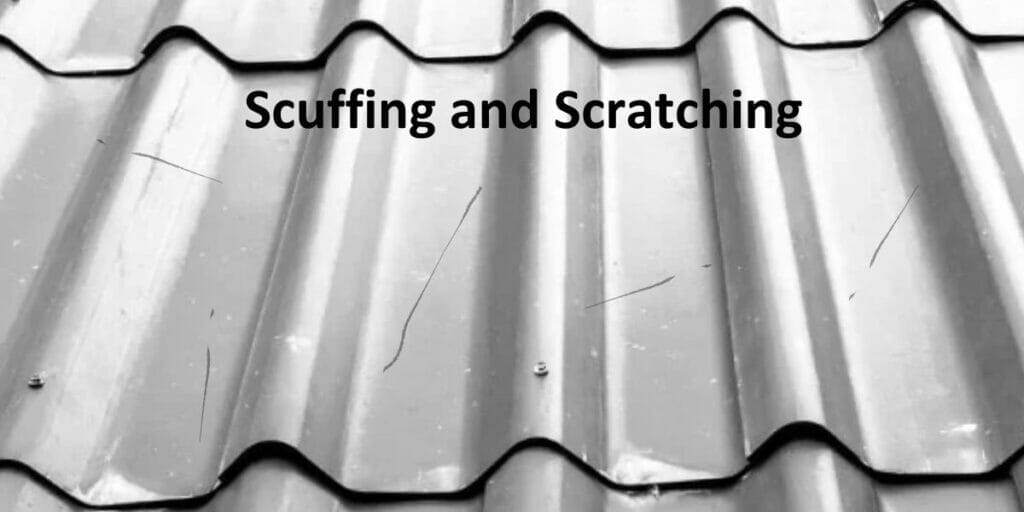
Metal roofs are at risk for scuffing and scratching, which can occur during transportation, roll-forming, or installation. Surface damage can be prevented by handling panels with proper lifting devices, using edge guards to protect the metal roof edges during transportation, maintaining roll-forming machines to prevent malfunctioning, and properly coiling and recoiling of the metal.
Solution: Fortunately, scratches and scuffs can be easily touched up with paint pens, which can fill, seal, and repair the damage. Also, avoid carelessly walking on metal roofing panels, and trim any overhanging tree branches that could scratch the material.
#4 Corrosion
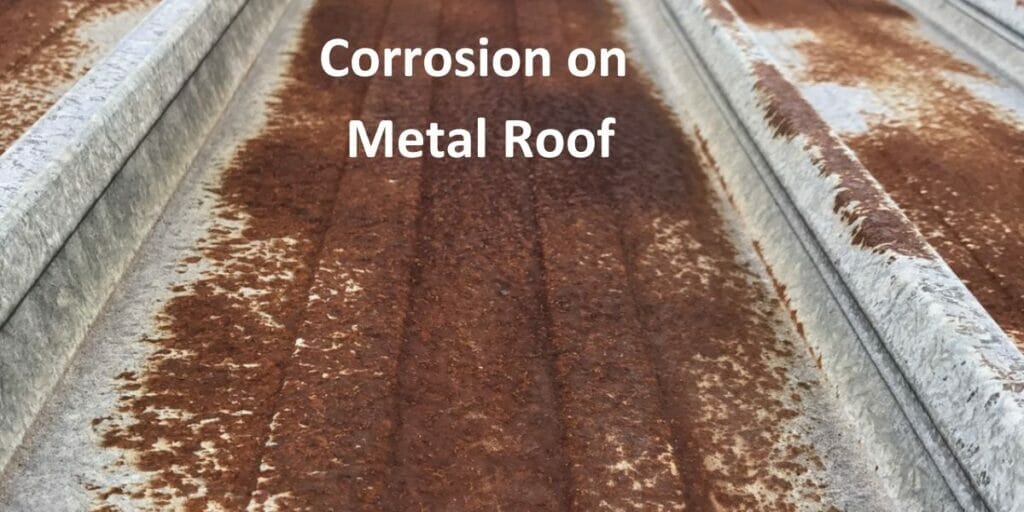
Corrosion occurs when an iron alloy reacts with oxygen in the air, or water, to form an oxide compound. Corroded metal is weaker and can easily puncture or tear off the roof, leading to water leakage. Metal roof corrosion can be caused by ponding, the metal coming into contact with a different material, and damages or punctures exposing the inner surfaces of the metal.
Solution: To reduce the risk of corrosion, keep the roof clean, ensure proper drainage, paint the roof to provide a protective coating over the metal, and use coated metal sheets that don’t rust easily.
#5 Chalking and Fading

Chalking is a white residue that appears on a painted or coated metal roof panel due to the breakdown of paint resin after prolonged sun exposure. Fading occurs when the paint’s pigment breaks down due to increased contact with UV rays, water, pollution, or chemicals. Metal roofs are at risk of uneven fading, as different panels are exposed to different levels of UV rays or other substances.
Solution: Talk to your roofing contractor about your chosen paint system’s warranty in case of fading, and utilize roof coatings to prevent this from occurring.
#6 Noisiness
Metal roofing is inherently noisier than other roofing materials, and this can be exacerbated by poor installation.
Solution: The noise can be minimized by ensuring a professional roof installation, insulating the home adequately, and using high-quality underlayment to minimize noise transmission. There are also specific types of materials that are more soundproof than others, depending on your personal preferences.
#7 Punctures and Tears
Metal roofs can be easily punctured and torn, exposing the roof to further risks such as leaks and wind damage. Punctures and tears can be caused by foot traffic, DIY repairs gone wrong, trees or tree branches falling on the roof, and faulty roof installations.
Solution: Avoid excessive walking on the roof, restrict rooftop installations to professionals, and trim trees around the house. If damage does occur, call for a repair as soon as possible before water leaks cause further damage.
#8 Fastener Back-Out
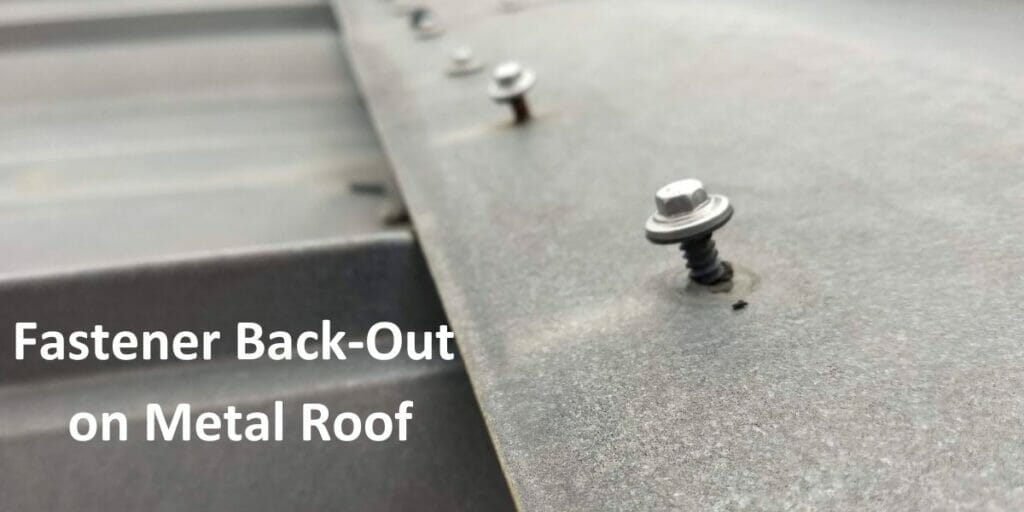
Fastener back-out is a common problem on metal roofs, which occurs when the fastener becomes loose and pulls out of the metal panel. This can be caused by metal panels expanding and contracting due to temperature changes, improper installation, and insufficient fasteners.
Solution: To prevent fastener back-out, use the right type and number of fasteners, install them at the correct spacing and length, and use screws with a neoprene washer to prevent water infiltration.
#9 Thermal Expansion and Contraction
Metal panels expand and contract because of temperature changes, which can cause problems such as fastener back-out and oil canning. This can be prevented by providing adequate space for thermal expansion and contraction during installation.
Solution: Make sure your metal roof is installed by knowledgeable and experienced roofing contractors who can provide adequate space for thermal expansion and contraction to occur without damage.
#10 Ice Damming
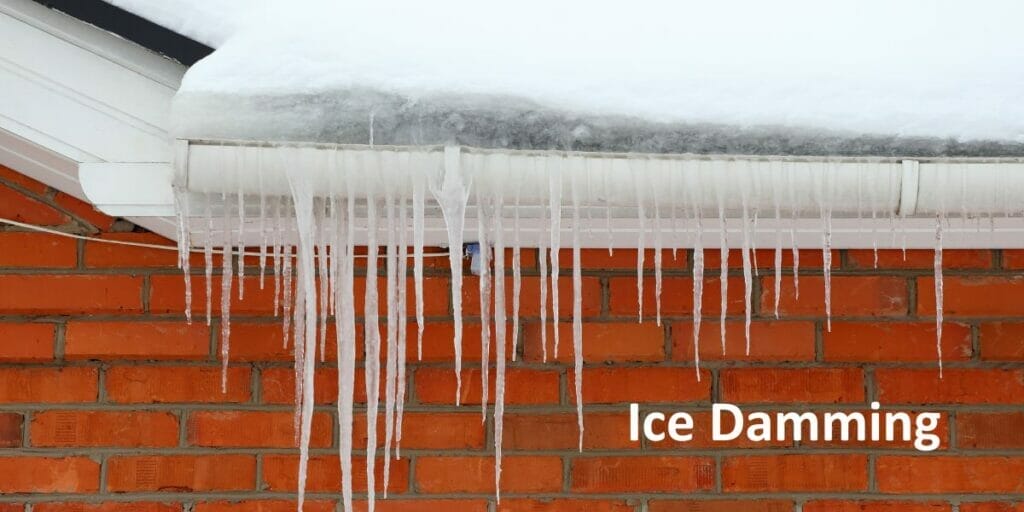
Ice dams are a problem that occurs on metal roofs when ice builds up on the roof and prevents water from draining properly. This can cause water to back up under the roof and leak into the home.
Solution: Ice damming can be prevented by ensuring proper insulation and ventilation of the roof, using a high-quality underlayment, and installing snow guards to prevent snow and ice from sliding off the roof in large sheets.
#11 Improper Installation
Improper installation is a common cause of metal roof problems, including leaks, oil canning, and fastener back-out. This can be avoided by ensuring your metal roof is installed by knowledgeable and experienced roofing contractors who follow manufacturer recommendations and guidelines.
Solution: Choose a reputable and experienced metal roofing company that can provide a lifetime, permanent metal roofing solution. Make sure to ask about their weather-tight warranty and follow their installation details to prevent future problems.
Conclusion
Understanding and addressing the common problems that can arise with your metal roof are essential for ensuring its longevity and durability. By exploring the top 11 metal roof problems and learning effective repair solutions, you have taken a proactive step towards safeguarding your investment. Remember, whether it’s dealing with leaks, rust, loose panels, or insulation issues, it’s always better to know how to handle the situation.
ReNew Roofing is a trusted and experienced company specializing in metal roof systems. Our team of experts can provide you with valuable guidance and professional assistance in resolving any metal roof problems you may encounter. With our expertise and your newfound knowledge, you can confidently tackle any challenge and maintain a sturdy, reliable, and long-lasting metal roof that will continue to protect your home for years to come. Don’t let metal roof problems dampen your spirits; instead, reach out to us at (813) 813-7663.
FAQs
A. While it is possible to manage water drainage without gutters, it is less effective and can lead to various issues, such as soil erosion, basement flooding, and damage to the home’s foundation and exterior.
A. Rain gutters collect rainwater and channel it away from the foundation, preventing soil erosion and potential foundation damage.
A. To maintain optimal water flow, gutters require regular maintenance, including cleaning out debris and ensuring they are free from clogs.
A. Rain gutters can be installed on most types of roofs, including sloped, flat, and metal roofs.
A. Gutters should be cleaned at least twice a year, usually in the spring and fall, to remove leaves, twigs, and other debris which can block water flow.
A. While DIY installation is possible, hiring a professional is recommended to ensure a proper installation and address any specific requirements of your home.
A. The lifespan of rain gutters can vary depending on the material and maintenance, but well-kept gutters can last for several decades.